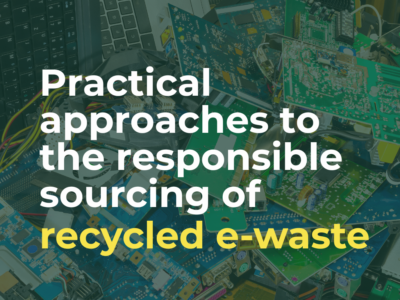
Practical approaches to the responsible sourcing of recycled e-waste
The future of clean energy lies in critical mineral production. An estimated three billion tonnes of minerals and metals will be required to produce the clean energy technology necessary to keep global warming below 2°C. To achieve this, production rates of some minerals may need to increase by up to 500 percent. The current global shortfall has led some observers to suggest that the Paris Agreement fired a starting gun in a new critical minerals arms race to ensure resilience of supply in the face of growing global protectionism and unstable geopolitics.
In this article TDi evaluates the potential for recycled materials to help meet the global critical mineral demand and examines the ESG issues in e-waste supply chains. We also take a look at the practical steps required to enable downstream companies to source secondary materials responsibly and make circularity an integral part of their responsible sourcing strategies.
E-waste | Facts and figures
The world generated 62 million tonnes of electronic waste (e-waste) in 2022, up from 53.6 million tonnes in 2019.2 Global e-waste is projected to reach 82 million tonnes in 20303 if current trends continue, making it the fastest growing waste-stream globally. In particular, it is thought that there were 80 million end of life vehicles (EoLVs) globally in 2020,4 representing both a growing waste challenge and opportunity,
Urban mining is the practice of reclaiming valuable materials from e-waste – providing an alternative to resource extraction and helping to create a circular economy. Urban mining exists both formally, through highly mechanised high-tech operations, and informally – on a smaller, unregulated scale. The recycling of e-waste through urban mining encompasses activities including the collecting of waste materials through to the processing of those materials and their re-entry into supply chains.
An under-utilised opportunity
Only 22.3% of the e-waste produced in 2022 was formally collected and recycled in an environmentally sound manner3 – leaving the majority unaccounted for – likely incinerated, dumped or processed informally. Despite growing political ambitions, the use of recycled materials has so far failed to keep pace with rising material consumption,1 due to a combination of factors including insufficient secondary feedstock, technological challenges and policy barriers.
Enhancing critical mineral recycling offers substantial sustainability benefits, with the International Energy Agency (IEA) indicating that the use of recycled energy transition minerals can result in 80% fewer greenhouse gas emissions on average than primary materials produced from mining.1 The use of secondary materials also reduces reliance on the development of new mines, and has the potential to enhance supply security for countries importing minerals. In addition, scaling up of recycling prevents waste from end-use technologies ending up in landfill.
Can urban mining fill the critical raw material gap?
According to the IEA, recycling is indispensable to the security and sustainability of minerals supply needed for clean energy transitions.1 Urban mining of these waste materials represents an important opportunity to capture secondary raw materials such as copper, aluminium, steel and rare earth metals.
Recycling of battery metals is an emerging commercial activity and growing fast (albeit from a low base), with the potential to meet 20-30% of lithium, nickel and cobalt demand by 2050 (assuming that collection rates improve).1 However, the EV battery sector has pivoted towards cheaper lithium-iron-phosphate (LFP) chemistry in the last couple of years, with such batteries now accounting for around 40% of the global market.6 This reduces the economic case for recycling, meaning that the sector may need to look at different pricing mechanisms for recycling.
What are the ESG issues associated with e-waste recycling?
While battery recycling presents a clear opportunity to meet the raw material gap, there are supply chain security issues in the battery recycling industry, and in light of current geopolitical tensions around trade tariffs, the risks associated with this have never been more apparent. China still dominates the middle processing part of the battery recycling supply chain, where recycled metals are fed back into precursor elements for new batteries. Today, the world’s top twenty countries for spent battery pre-treatment and materials recovery are all Chinese – which represents a potential dependency, and further risk to self-sufficiency in critical mineral supply.5
When it comes to EoLVs, efforts are increasing globally to improve the recovery of materials at end-of-life, particularly in countries with high imports of used vehicles. Ghana is one such example, where the informal sector currently collects more than 80% of e-waste, providing livelihoods, but also raising concern over environmental and labour rights. The story is the same in many low- and middle-income countries.
TDi’s Responsible Mining Specialist, Elizabeth Arnott worked on an urban mining project in Ghana in 2021, mapping supply chains, interviewing waste collectors and recyclers on the ground, and developing an understanding of where and how downstream companies could become engaged in the process. ‘Unregulated handling of e-waste can lead to pollution from drainage of battery acid, toxic dust and open burning of cables’ says Elizabeth. ‘Workers are exposed to hazardous chemicals, and in many cases lack suitable PPE, with unsafe dismantling practices endangering both workers and surrounding communities. Such informal urban mining networks operate outside of formal regulatory frameworks, making oversight of issues such as child labour, traceability and ethical sourcing in general, difficult.’
The business case for downstream companies
Integration of responsible urban mining into sustainability strategies can help downstream companies, such as those in the automotive and electronic industries, to meet their ESG requirements.
Policy momentum is also gaining strength, and the IEA has identified more than 30 new policy measures related to critical mineral recycling since 2022,1 many of these relating to Extended Producer Responsibility (EPR). EPR is a policy approach that makes producers responsible for their products along the entire lifecycle, including at the post-consumer stage. In recent years policymakers have increasingly embraced the EPR approach and the geographic scope of its use continues to grow, with more countries developing EPR systems. ‘Recycling of primary materials is now a core part of the conversation from a regulatory perspective’ says TDi Sustainability Consultant, Joséphine Quioc. ‘With targets around recycled content in both the EU Battery Regulation and Critical Raw Materials Act, it’s important that companies consider how they will meet upcoming targets around the requirement for recycled content.’
The role of downstream companies in improving traceability
With the current shift in focus to securing critical mineral supply chains, driven by increasing geopolitical tensions, Elizabeth and Joséphine believe that the time is ripe to re-address engagement in formalisation of the recycling of e-waste.
‘Disengagement from potentially risky sources of recycled materials doesn’t help to address the root causes of the risks faced by workers in the informal sector, and could put thousands of people out of work, potentially increasing opportunities for exploitation and deepening supply chain opacity’ explains Elizabeth. ‘In line with TDi’s experiences in working with artisanal and small-scale mining communities alongside The Impact Facility and the Fair Cobalt Alliance, we believe that the responsible and productive way forward is to engage by helping to support safer and fairer practices, working towards formalisation of the sector as a safe and dignified livelihood, rather than avoiding the sourcing of recycled materials from small-scale operations.’
By supporting responsible urban mining practices to secure secondary raw materials, downstream companies can simultaneously address ESG risks in their supply chains in line with their sustainability strategy. But what does this mean in practice? ‘There are lots of ways that downstream companies can support the development of a responsible urban mining ecosystem’ says Joséphine. ‘As a basic starting point, it’s important for companies to identify any sources of recycled materials in their supply chains, or where they could look to include more recycled materials. The development of a mine-market model or strategy, similar to that produced for material supply from primary mining operations can help bring greater transparency and accountability to material sourcing. Once you understand where the materials in your products have originated from, look at how you can engage with programmes that exist locally to support the formalisation of scrap initiatives. This can help in the creation of fair pricing models and worker safety improvements.’
Collaboration between public and private sectors and industry participation in international consortiums and in the development of government policy can also help to drive scalable solutions. ‘We’re seeing this type of approach in Chile with the recovery of cobalt from mine tailings’ says Elizabeth. ‘Alternative supply chain models such as book-and-claim systems successfully implemented in sustainable palm oil and soy could also be adapted for urban mining.’
Alongside local and public-private sector initiatives, it’s essential that governments and NGOs continue to invest in infrastructure and regulatory frameworks to formalise and improve urban mining conditions in countries such as Ghana. ‘To support this, consumers and businesses alike have an important role in advocating for increased transparency in e-waste management and recycling initiatives’ finishes Elizabeth.
Conclusion
While urban mining does not eliminate the need to source primary materials, it’s clear that increasing circularity through recycling of e-waste can create a valuable secondary supply source of critical minerals that reduces reliance on new mines and enhances supply security for importing countries and businesses.
However, it’s important to understand that there are also environmental, social and governance issues associated with recycling activities if these activities are not formalised or regulated. It’s therefore essential that companies conduct appropriate due diligence on both their primary and secondary sources of critical minerals, and engage in and support the development of responsible supply chains across all of their material sourcing.
TDi Sustainability can help to identify suppliers of secondary critical minerals in your supply chain as well as opportunities for increased circularity within your responsible sourcing strategy to help you meet upcoming regulatory targets. Our experts can help you to understand and mitigate the environmental, social and governance risks associated with the sources of those materials. We can also help you to identify and develop programmes that support local communities in the formalisation of the e-waste collection and recycling process, and increase the long-term sustainability and resilience of your business operations.
1 IEA (2024), Recycling of Critical Minerals, IEA, Paris https://www.iea.org/reports/recycling-of-critical-minerals, Licence: CC BY 4.0
2 Balde CP, Kuehr R, Yamamoto T, McDonald R, D’Angelo E, Althaf S et al. The Global E-waste Monitor 2024. Bonn, Geneva: International Telecommunication Union, United Nations Institute for Training and Resources; 2024 (https://ewastemonitor.info/).
3https://www.weforum.org/stories/2024/04/e-waste-recycling-electronics-appliances/
4 Petronijević, V.; Đorđević, A.; Stefanović, M.; Arsovski, S.; Krivokapić, Z.; Mišić, M. Energy Recovery through End-of-Life Vehicles Recycling in Developing Countries. Sustainability 2020, 12, 8764. https://doi.org/10.3390/su12218764
5 https://www.reuters.com/markets/commodities/us-targets-scrap-close-critical-minerals-gap-andy-home-2024-11-27/
6 https://www.iea.org/reports/global-ev-outlook-2024/trends-in-electric-vehicle-batteries